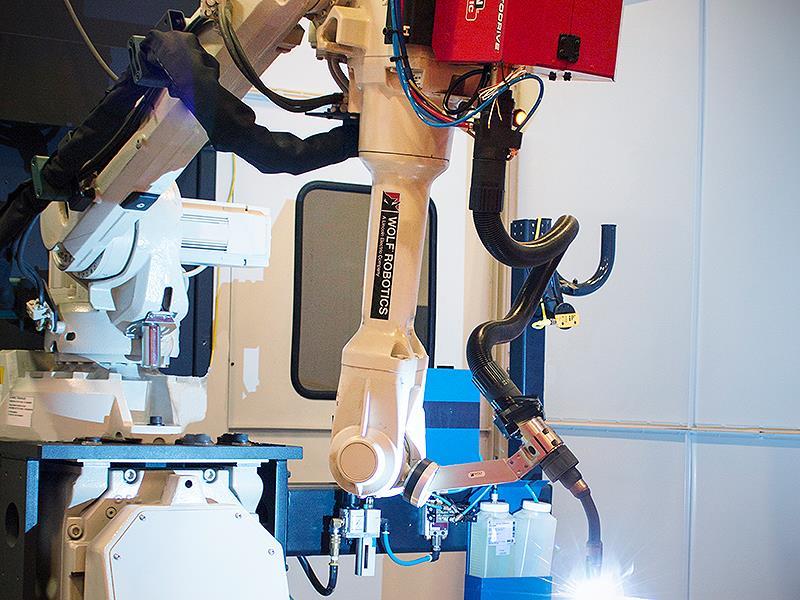
Industrial Robots: Trends and Prospects
Today, industrial manipulation robots are used in almost all large-scale machine building industries. The lion’s share of complex engineering products is produced not by humans, but by automatic machines.
They manufacture individual parts, assemble finished products from them, check the quality of products, load them onto vehicles or send them to storage. Automation is one of the leading directions of Russian industry modernization.
Industries where robotic equipment is most actively used include the following:
- the car industry;
- machine-tool construction;
- Installation of radio equipment;
- food industry.
The list is far from exhaustive. A significant advantage of robotics is its versatility – it can be implemented almost everywhere, including human life (“Smart Home” systems). Therefore, to this list can be added any other areas of life, up to medicine.
Availability of equipment
The main prerequisite for the active introduction of industrial robotic manipulators was a reduction in their price, which previously accounted for almost half of the cost of the entire enterprise. Previously, the installation of automatic systems could only be afforded by large plants, such as the military or any other state-owned and financed plants.
In contrast to the past, the price of modern machine-building automation is affordable even to medium-sized companies, which only need to take a small loan. Another question is to what extent automation is effective from an economic point of view.
Costs associated with the purchase of automation are expedient only if the production of large batches of products is planned. When producing medium batches, economic efficiency is already on the verge of profitability and loss-making. And for small-batch production, this indicator is almost always negative, at least at the beginning of the activity.
If it is planned to produce several thousand or tens of thousands of products, the use of automatic machines is economically justified, helping to save money. In contrast to people technical means are capable to function round the clock.
They work without wages and a social package, they do not need sick leave or vacation at their own expense. Statistics show that the introduction of automatic assembly lines allows you to save up to 25-30% of the company’s budget, which increases the profitability of the production business.
Easy operation
Reducing the cost of robotics is the main factor, but not the only one, in the intensive spread of robotics. Simplifying the operation of robotics also plays a significant role.
Ensuring normal operation no longer requires the involvement of a whole staff of system engineers. Machine control and programming of industrial robots can be carried out by almost any specialist with basic technical skills.
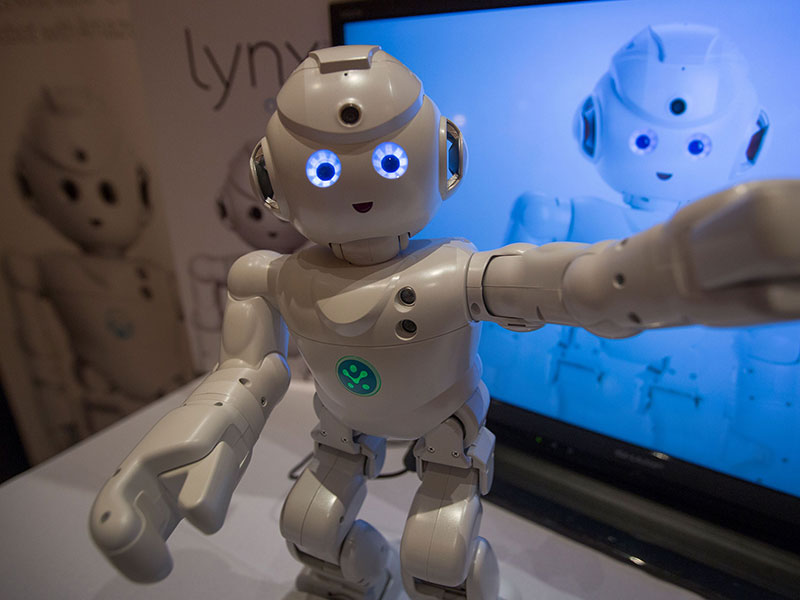
Types of industrial robots
There are several types of industrial robots that are classified according to the following criteria:
- type of operations (universal, special, specialized robots);
- Load capacity (light, medium, heavy);
- degree of freedom of manipulation (single- and multi-axis);
- method of installation (floor, suspended, built-in).
In addition, all machines differ in their type of control, which can be programmatic or adaptive. In the first case, the equipment is controlled by the software.
These devices accurately execute the programmed program. Machines of the second type – with adaptive control – can be called trainee machines. Before the start of the work, the operator guides the implements through a series of intermediate positions. Each point is fixed by the equipment memory.
The automated system, as a matter of fact, forms the program itself, however, with participation of the person. Then it functions without external interference. If necessary, it is relatively easy to change the algorithm by reconfiguring the technique to perform other actions.
Production of industrial robots
Japan, Germany and the United States are among the leaders in the production of industrial robots. However, Russian-made industrial robots are produced. This cluster is represented in our country by two companies – Record Engineering (Ekaterinburg) and Arkodim (Kazan).
Moreover, if the Urals company performs screwdriver assembly of imported equipment of different brands, the Kazan company develops its own models, cooperating with scientific laboratories of Novosibirsk, Moscow and the Russian “Innograd” Skolkovo.
Domestic developers strive for indicators that will allow to replace 100% Japanese and German analogues. Our manufacturers are able to change the situation by introducing new and more flexible control systems, increasing the productivity of machines, improving actuators. Key priorities include reducing overall size, ease of use and maintenance, and improving energy efficiency.
A powerful incentive for the domestic robotics industry may be an increase in demand for equipment from the industry. If industrial robots are in demand by machine-building plants, it will give an additional impetus to the work of existing companies, as well as initiate the emergence of other manufacturers producing automated systems for machine-assembly operations.